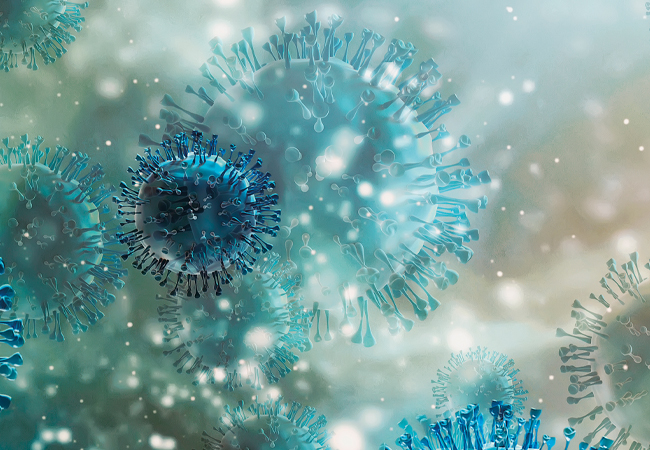
Six companies will be in contention for CIBSE’s top accolade for air quality products and innovations at this month’s Building Performance Awards. A diverse array of products is on the shortlist for the Product or Innovation of the Year – Air Quality award, open to entries that significantly enhance the air qualityaspect of building performance.
The judges said the entries not only showcase a breadth of innovation, but also reveal a keen understanding of the importance of application flexibility while adhering to stringent regulatory standards. They were impressed by the calibre of the shortlist, saying ‘the range of innovations demonstrates that the product doesn’t have to be epic to be influential and beneficial’.
The CIBSE Building Performance Awards will take place on 29 February 2024 at the Park Plaza Westminster Bridge Hotel in London. To book your place visit bit.ly/CIBSEbpa24.
Stiebel Eltron UK: VLR 70 L Trend
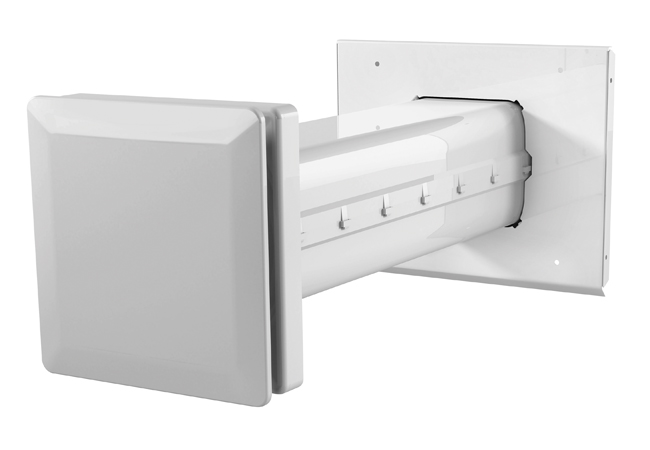
Stiebel Eltron UK introduced its VLR 70 L Trend, a decentralised ventilation unit, in response to the need for landlords and property owners to implement measures to deliver good air quality in social housing and commercial properties. This fully automated unit improves indoor air quality, reduces moisture, and recovers up to 92% of heat, in spaces up to 100m2.
Installed in pairs – either in one or adjoining rooms with good airflow between them – one unit will extract while the other brings in fresh air. The units switch several times a minute between each other to allow the heat exchanger to capture energy from the outbound air, which is then picked up by the incoming air. The unit incorporates smart sensors to account for occupancy, humidity and air quality. With a comprehensive filter system, including F7 filters, the VLR 70 L reduces pollutants, allergens and virus particles.
Vent-Axia: Sentinel Apex
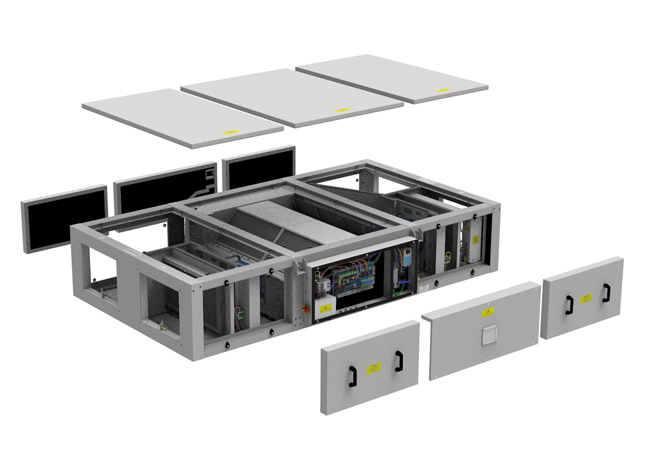
Vent-Axia’s Sentinel Apex commercial heat recovery unit provides fresh, filtered air, combating indoor air pollution and removing pollutants such as moisture and CO2. With up to 93% energy recovery, the unit efficiently uses waste heat, achieving a market-leading 93% thermal efficiency (EN308 tested). Key features include an automatic summer bypass, motor efficiency equivalent to better than IE5 efficiency class, demand control for optimising IAQ, and ultra-low sound levels.
The system was designed for adaptability, energy conservation, and personalised comfort. Vent-Axia’s in-house testing facility and market research informed the unit’s development, focusing on low specific fan power, efficiency, and low sound levels. The unit, which has been specified but not yet installed, is expected to deliver high performance in diverse climates, addressing the demand for sustainable, energy-efficient building solutions.
Glazpart: Link Vent 4000
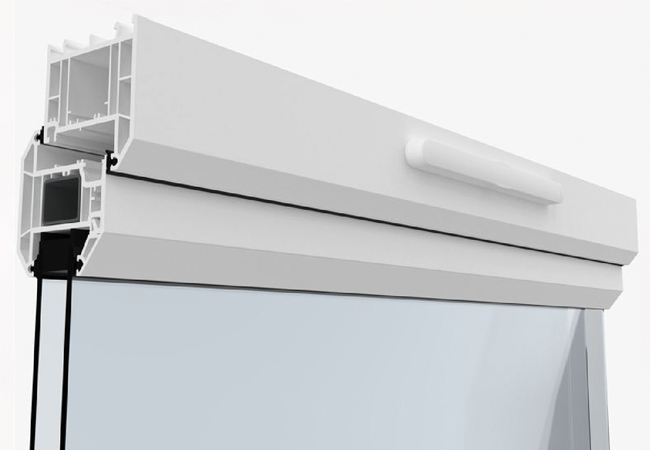
The Link Vent 4000, a trickle vent for windows and doors to facilitate passive airflow in dwellings, has received excellent feedback for its simple, user-friendly design. An equivalent area of 4,000mm2 is delivered through a 167mm x 13mm slot, reducing routing machine times and waste materials generated. Further increasing its versatility, the Link Vent 4000 can cool a house when overheating or moderate temperatures through smart ventilation when properties become cold and heating is turned on.
The closing action allows more control over draughts by directing air away from occupants, and the split closure plate enables partial opening. The system was created to address the need for ventilation in smaller rooms and aligns with the 2022 legislative changes. Fully compliant with the Building Regulations, the vent enhances air quality and prevents overheating, and received positive feedback from industry leaders.
Daikin: VRV 5 Heat Recovery

Daikin’s VRV 5 Heat Recovery system is a sustainable and efficient HVAC solution for commercial buildings. Its three-pipe heat recovery technology allows simultaneous cooling and heating, enhancing efficiency with a low condensing temperature. The system includes Daikin’s Shîrudo technology, which uses the integration of a sensor, shut-off valves and alarm to detect and isolate potential leaks. Daikin says this enables rooms to be tackled as small as 10m2 without additional calculations or measures.
Daikin also offers embodied energy assessments for the system based on the TM65 calculation methodology. It shows a decrease of up to 53% in embodied carbon. Case studies, such as the University of Lincoln and BBC Earth Experience, showcase successful installations, highlighting the environmental considerations and energy efficiency.
Kampmann UK:WZA – Decentralised Scholl Ventilation Unit
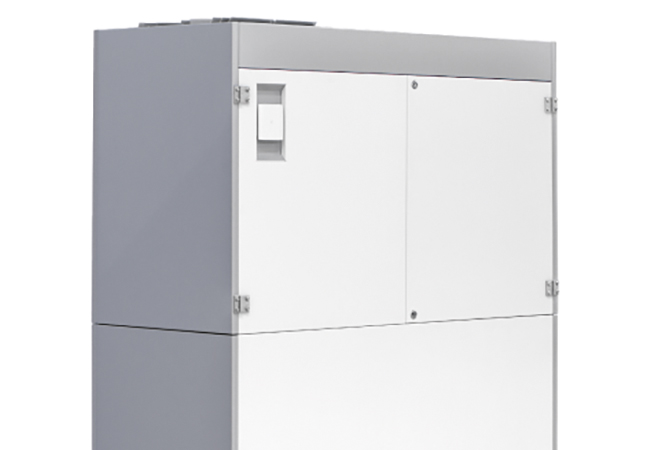
This unit, introduced to the continental European market in late 2021, enhances air quality and minimises virus concentration. It is designed to improve indoor air quality in classrooms, where research has found that elevated CO2 levels can hinder concentration. With a maximum airflow of 280l/s, the WZA unit features automatic airflow control based on CO2 levels, ensuring it stays below a programmed concentration.
Equipped with an enthalpy counterflow plate heat exchanger, the unit efficiently recovers thermal energy and optimises humidity levels, which is particularly beneficial in winter. Operating on mixed-air ventilation principles, it introduces supply air without draughts. The company focuses on minimising whole life carbon, and the WZA materials are designed to be easily taken apart and separated for recycling.
Healthy Air Technology: Distributed Air Purification System
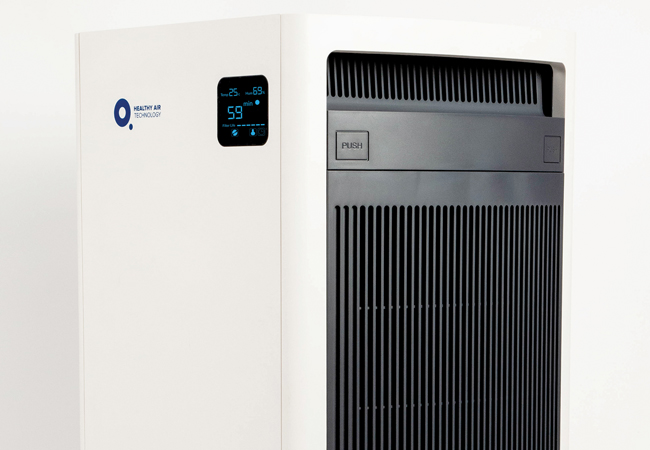
This holistic air purification solution, integrated with BlockDox buildin management systems, takes a novel approach to combine indoor air quality and building performance. By pairing the HA800 air purification technology with BlockDox’s IoT-enabled platform, the solution optimises spaces for health, comfort, and energy efficiency.
The HA800’s multi-layered filtration system captures pollutant particles as small as 0.3 microns, ensuring clean, healthy air. Its closing action controls draughts, and a split closure plate enables partial opening for enhanced user control. By integrating real-time data from the air purifiers and other building systems, BlockDox’s platform empowers precise and responsive management of environments. It is user-friendly and easy to maintain.